Using laminating film on model aircraft surfaces
In this article, we'll be using laminating film to strengthen and seal the vertical stabilizer and rudder from a QuickFlick-II discus launch glider, complete with a live hinge. Laminating film is a very low cost replacement to the more expensive coloured plastic covering films. Laminating film has many advantages over coloured plastic covering films including tensile strength. This small article will show you how to easially use laminating film to cover flat, sheet or open-frame surfaces quickly, cleanly and with good results.
With laminating film being so cheap it opens up new ways to use it for covering which are considered too wasteful in comparison to normal model aircraft covering films. The process used here creates a medium amount of wastage but the quality of the results and the low financial hit is insignificant. Using the method detailed here, you can also produce live-hinges that will last for a very long time.
Required materials:
- Laminating film (40 micron for small surfaces, 80 for larger)
- Household iron (set to cotton or linen)
- Heat gun (optional)
- Sheet of glass (6mm or thicker preferred)
- Sharp knife (No.11 blade preferrable)
- Clear tape (for opposite side of live hinge - if required)
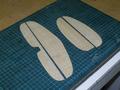 |
Prepare your raw surfaces
The smoother your can get your raw balsa flying surfaces the stronger the overall adhesion will be with the film. In this case, the QFII uses 1.5mm balsa which has been shaped and sanded back with 400 grit paper. We will be using 40 micron film for this job.
|
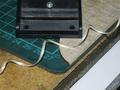 |
Apply hinge bevel
If you're wanting to use the laminating film as a live hinge, then you will need to bevel one of the two parts at about 45 degrees. To do this you can either use a razor plane (pictured) or a sanding bar. |
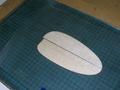 |
Position surfaces and lay over film
Place the tail surfaces on the glass as required. If you're going to be doing a hinged surface then have about a 0.5mm gap between the two parts.
The 0.5mm gap is to allow for the hinge material on the opposite side to fit (without binding).
Lay the laminating film over the positioned parts with the adhesive (matt/rough) side down. Ensure there's at least 40mm of excess laminating film all around.
|
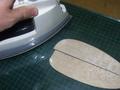
|
Tack down laminating film
Using the household iron, set to cotton/linen, seal down the excess film around the surfaces. This will start to pull the film taut. Don't worry about small wrinkles.
|
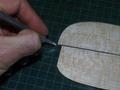 |
Create an exhaust hole in the film
Because of the heat from the iron and the shrinking film, trapped air will prevent the film from smoothly sticking to the surfaces. Cut a small L notch in the film near the edge of the surface (so that the hole allows the air to escape).
|
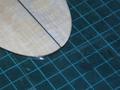
|
Tack film to around the perimeter of the surfaces
Before doing the final adhesion of the film to the surfaces, run the edge of the iron all around the perimeter of the surface. This will pull the
film across the surface rather tightly. DO NOT yet run the iron across the actual balsa surface, that happens in the next step.
|
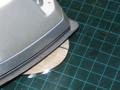
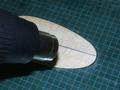
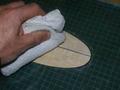 |
Bonding the laminating film to the balsa surface
Finally the real process starts. Using either a heat gun or house iron, shrink the laminating film covering the surface and immediately
rub it down hard with a soft cloth to enhance the bond.
You may notice at this point that the balsa surface will curl up, do not worry about this, it's caused by the heat driving the moisture out of one side of the balsa.
It will be corrected when you apply the film to the other side.
|

|
Cut out the balsa surface
Using a sharp knife, cut out the balsa surface from the laminating film. Cut slightly wide so as to provide a small amount of unbonded laminating film which
will be tacked down by the iron - this is so the laminating film will go around the edges and overlap (with the opposite side).
|
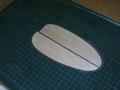
|
Turn over surface and repeat
Repeat the above process for applying the laminating film for the other side.
|
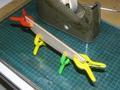
|
Hinging the tail
After both sides have been laminated you will need to cut clear the excess laminating film that bridges across the open side of the bevelled hinge.
Once the excess has been cut away you should be able to move the hinged surfaces normally. For very very light load situations having one side
hinged may be sufficient however it's often best to double-side the hinge.
- Fold the hinged surfaces back, exposing the bevelled edge.
- Align the bevelled edge and the square face of the opposite part.
- Apply a strip of tape across the two
- Trim off excess tape from both ends and check the hinge.
|
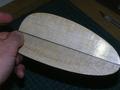
|
Admire finished product
Your hinged surface is now complete. Not only is the resultant product stiffer than the raw balsa item, it should also be considerably less draggy.
Enjoy!
|
|